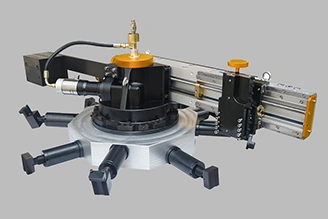
Keyword: Flange facing machine
html
Flange Facing Machine: Essential Tool for Precision Surface Finishing
In the world of industrial machining and metalworking, achieving a perfect surface finish is crucial for ensuring the longevity and efficiency of components. One of the most indispensable tools for this purpose is the flange facing machine. Designed to deliver precision and consistency, these machines are widely used across various industries, including oil and gas, power generation, and shipbuilding.
What is a Flange Facing Machine?
A flange facing machine is a specialized piece of equipment used to machine the surfaces of flanges to ensure they are perfectly flat and smooth. Flanges are critical components in piping systems, as they provide a secure connection between pipes, valves, and other equipment. Any imperfections on the flange surface can lead to leaks, reduced efficiency, or even catastrophic failures. The flange facing machine eliminates these risks by providing a high-quality finish.
Key Features of Flange Facing Machines
Modern flange facing machines come equipped with advanced features to enhance performance and ease of use. Some of the key features include:
- Portability: Many models are designed to be lightweight and portable, allowing for on-site machining without the need to disassemble piping systems.
- Precision Cutting: These machines use high-speed cutting tools to achieve micron-level accuracy, ensuring a flawless surface finish.
- Versatility: They can handle a wide range of flange sizes and materials, from stainless steel to cast iron.
- Automation: Some advanced models feature automated controls for consistent and repeatable results.
Applications of Flange Facing Machines
Flange facing machines are used in a variety of applications where precision surface finishing is required. Some common uses include:
- Pipeline Maintenance: Ensuring flanges are properly machined to prevent leaks in oil and gas pipelines.
- Power Plants: Maintaining the integrity of flanges in high-pressure steam and water systems.
- Shipbuilding: Machining flanges for marine piping systems to withstand harsh conditions.
- Chemical Processing: Providing corrosion-resistant finishes for flanges used in aggressive chemical environments.
Benefits of Using a Flange Facing Machine
Investing in a high-quality flange facing machine offers numerous benefits, including:
- Cost Savings: On-site machining reduces downtime and eliminates the need for costly replacements.
- Improved Safety: Properly machined flanges minimize the risk of leaks and failures.
- Enhanced Efficiency: Smooth flange surfaces ensure optimal sealing and system performance.
- Longevity: Precision finishing extends the lifespan of flanges and associated equipment.
Conclusion
The flange facing machine is an essential tool for any industry that relies on precision surface finishing for flanges. Its ability to deliver consistent, high-quality results makes it a valuable asset for maintenance and repair operations. Whether you’re working in oil and gas, power generation, or shipbuilding, investing in a reliable flange facing machine can significantly improve your operational efficiency and safety.