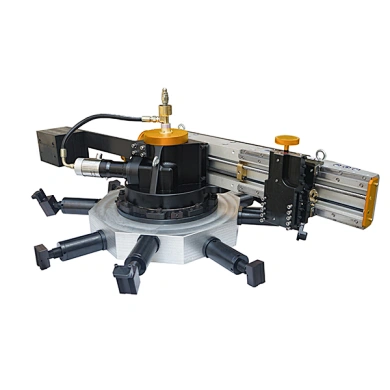
# Industrial Flange Facer: Essential Tool for Precision Machining
## Introduction to Industrial Flange Facers
In the world of industrial machining and pipe fitting, precision is paramount. The industrial flange facer has emerged as a critical tool for ensuring perfect mating surfaces on flanges, enabling leak-proof connections in high-pressure systems. These specialized machines have revolutionized the way maintenance teams and fabricators approach flange preparation.
## What is a Flange Facer?
An industrial flange facer is a portable machining tool designed to resurface flange faces directly on-site or in the workshop. Unlike traditional machining methods that require removing flanges from pipelines, these innovative tools allow for in-situ repairs and surface preparation. They typically consist of a rigid frame, cutting tools, and precise adjustment mechanisms to achieve the required surface finish.
## Key Features of Modern Flange Facers
Today’s advanced flange facers incorporate several important features:
- Portable designs for field use
- Precision cutting tools with adjustable feed rates
- Versatile mounting systems for different flange sizes
- Digital readouts for accurate depth control
- Durable construction for industrial environments
Keyword: Industrial flange facer
## Applications Across Industries
Oil and Gas Sector
In refineries and pipelines, flange facers ensure proper sealing of high-pressure connections, preventing dangerous leaks and maintaining operational safety.
Power Generation
Power plants rely on precisely faced flanges for steam systems and other critical connections where even minor imperfections can lead to significant efficiency losses.
Chemical Processing
The chemical industry benefits from flange facers when dealing with corrosive materials that require perfect sealing to prevent hazardous leaks.
## Benefits of Using a Flange Facer
The advantages of incorporating a flange facer into maintenance operations are numerous:
- Reduces downtime by enabling on-site repairs
- Eliminates the need for complete flange replacement
- Provides superior surface finish compared to manual methods
- Cost-effective solution for maintaining pipeline integrity
- Improves safety by ensuring proper sealing surfaces
## Choosing the Right Flange Facer
When selecting an industrial flange facer, consider these factors:
- Maximum and minimum flange size capacity
- Power source requirements (electric, hydraulic, pneumatic)
- Cutting tool options and replacement availability
- Portability and setup time
- Compatibility with different flange standards (ANSI, DIN, etc.)
## Maintenance and Care
To ensure long-term performance of your flange facer:
- Regularly clean and lubricate moving parts
- Inspect cutting tools for wear and replace as needed
- Store in a dry, protected environment
- Follow manufacturer’s maintenance schedule
- Train operators in proper use and handling
## Future Trends in Flange Facing Technology
The industrial flange facer continues to evolve with new technological advancements:
- Integration with digital measurement systems
- Automated cutting processes with CNC-like precision
- Lightweight composite materials for improved portability
- Smart sensors for real-time performance monitoring
- Enhanced safety features for hazardous environments
## Conclusion
The industrial flange facer has become an indispensable tool for maintenance teams and fabricators across numerous industries. By providing precise, on-site machining capabilities, these tools save time, reduce costs, and improve the reliability of critical piping systems. As technology advances, we can expect even more