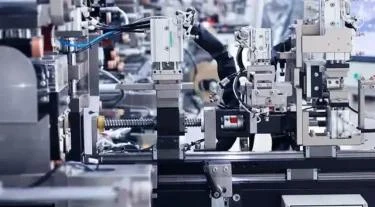
# Tape Production Process and Techniques
## Introduction to Tape Manufacturing
Tape manufacturing is a complex process that involves multiple stages to create adhesive products for various applications. From everyday household tapes to industrial-strength adhesives, the production techniques have evolved significantly over time to meet diverse consumer and industrial needs.
## Raw Materials Selection
The foundation of quality tape production lies in careful selection of raw materials:
– Backing materials (paper, plastic films, cloth, or foil)
– Adhesive compounds (rubber-based, acrylic, or silicone)
– Release coatings
– Additives for specific properties
## The Tape Production Process
### 1. Backing Material Preparation
The process begins with preparing the backing material. Plastic films are typically extruded, while paper and cloth backings undergo special treatments to enhance strength and adhesive compatibility.
### 2. Adhesive Application
There are several methods for applying adhesive:
– Solution coating: Adhesive dissolved in solvent and applied
– Hot melt coating: Molten adhesive applied directly
– Water-based coating: Environmentally friendly alternative
### 3. Drying Process
After application, the adhesive must be properly dried:
– Solvent-based adhesives require extensive drying to remove solvents
– Water-based systems need controlled evaporation
– Hot melt adhesives cool and solidify naturally
### 4. Lamination and Winding
The finished tape is laminated with release liners if needed, then wound onto cores for final packaging. Precision winding ensures uniform tension and prevents deformation.
## Specialized Tape Manufacturing Techniques
### Pressure-Sensitive Tape Production
This common tape type uses viscoelastic adhesives that bond under light pressure. The manufacturing focuses on achieving the right balance between tack, peel strength, and shear resistance.
### Double-Sided Tape Manufacturing
Requires precise application of adhesive on both sides with proper release liners. Special techniques ensure proper alignment and prevent adhesive transfer.
### High-Temperature Tape Production
Incorporates specialty adhesives and backings that withstand extreme temperatures. Silicone-based adhesives and fiberglass backings are common for these applications.
## Quality Control in Tape Manufacturing
Rigorous testing ensures product consistency:
– Adhesion strength measurements
– Tensile strength testing
– Temperature resistance evaluations
– Aging and durability studies
## Environmental Considerations
Modern tape manufacturing emphasizes sustainability:
– Reduction of solvent use
– Development of biodegradable adhesives
– Energy-efficient drying systems
– Recycling programs for production waste
## Future Trends in Tape Production
Emerging technologies are shaping the future of tape manufacturing:
– Nanotechnology-enhanced adhesives
– Smart tapes with sensing capabilities
– Bio-based adhesive formulations
– Automated production with AI quality control
The tape manufacturing industry continues to innovate, developing new products that meet evolving market demands while addressing environmental concerns. From everyday household applications to specialized industrial uses, the science of tape production remains a fascinating field of material engineering and manufacturing technology.
Keyword: tape manufacturing